Exploring the full supply chain of the mining industry and the critical role of ore mixing in optimizing costs and meeting customer demands.
Optimizing the Mining Supply Chain with Ore Mixing: Challenges and Solutions
🌍 The Full Supply Chain of the Mining Industry
In the mining industry, the process from extraction to final sale involves multiple intricate stages.
Each stage plays a crucial role in ensuring that raw materials are transformed into finished products efficiently.
Here’s an overview of the entire supply chain:
- Exploration and Assessment
- Conduct geological surveys and resource evaluations to determine the mineral reserves and quality.
- Extraction and Processing
- Extract minerals through open-pit or underground mining methods.
- Perform initial processing like crushing and screening to enhance mineral grade.
- Transportation and Storage
- Transport processed minerals to warehouses or ports for further handling or direct sale.
- Sales and Customer Communication
- Engage with customers to understand their specific requirements regarding mineral composition and quantity.
- Blending Calculation and Procurement
- Based on customer needs, calculate the optimal blending ratios.
- Procure the necessary ores.
- Blending and Production
- Mix different types of ores according to the calculated ratios.
- Produce a blended product that meets customer specifications.
- Delivery and After-sales Service
- Deliver the blended ore to customers.
- Provide necessary after-sales support and technical assistance.
🏭 What is Ore Blending and Where Does It Fit?
- Ore blending refers to the process of combining ores from different sources with varying compositions to meet specific customer requirements.
This step typically occurs during the blending calculation and procurement phase. - When customers specify particular mineral content requirements that cannot be met by a single ore type, blending becomes essential.
For example, in iron ore trading, customers may require a specific iron content range that existing inventory cannot fully satisfy.
In such cases, blending adjusts the iron content to meet these specifications.
✅ The Role and Benefits of Ore Blending
- Key Functions:
- Meeting Customer Specifications: Blending ensures that the final product precisely matches the client's requirements.
- Cost Optimization: By selecting the most economical combination of ores based on market prices and inventory, companies can reduce procurement costs.
- Enhancing Competitiveness: Rapid response to market demands and customized solutions strengthen market position.
- Advantages:
- Cost Savings: Automated tools like MixOrePlan quickly find the best blending ratios, reducing manual errors and saving significant time and money.
- Increased Efficiency: Handling large datasets swiftly leads to faster decision-making.
- Quality Assurance: Ensures consistent quality, minimizing variations caused by human error.
- Environmental Sustainability: Efficient use of existing stock reduces unnecessary mining and waste.
❌ Current Challenges in Ore Blending
Despite its importance, ore blending faces several challenges:
- Complex Calculations: Manual calculations involving multiple variables are time-consuming and prone to errors.
- Lack of Transparency: Traditional methods often lack transparency, making it difficult for stakeholders to understand the logic behind decisions.
- Dependency on Expertise: Relying on experienced personnel limits flexibility and increases operational costs.
- Market Volatility: Frequent price fluctuations make it challenging to maintain cost-effective strategies using traditional methods.
💻 How Automated Calculation Tools Can Save Millions
To address these challenges, we developed MixOrePlan, an automated tool specifically designed for the mining industry.
This tool offers a robust solution for efficient ore blending.
- Features
- Rapid Calculation: Users input the desired blend specifications and raw ore data, and the tool instantly computes the optimal blending ratio.
- Cost Minimization: Advanced algorithms identify the most cost-effective combinations, significantly lowering procurement expenses.
- Transparency and Clarity: Detailed reports explain each step of the calculation, ensuring results are easily understood.
- Real-time Updates: Incorporates current market prices to ensure calculations are always up-to-date.
- Impact
- For a company purchasing 1 million tons of ore annually, MixOrePlan can save between $3 million and $5 million per year.
This translates to substantial cost savings over time, enhancing profitability and competitiveness.
In summary, MixOrePlan bridges the gap in complex industrial calculations, providing a reliable and innovative solution that optimizes costs and improves efficiency.
For mining professionals and companies, this tool is indispensable.
- For a company purchasing 1 million tons of ore annually, MixOrePlan can save between $3 million and $5 million per year.
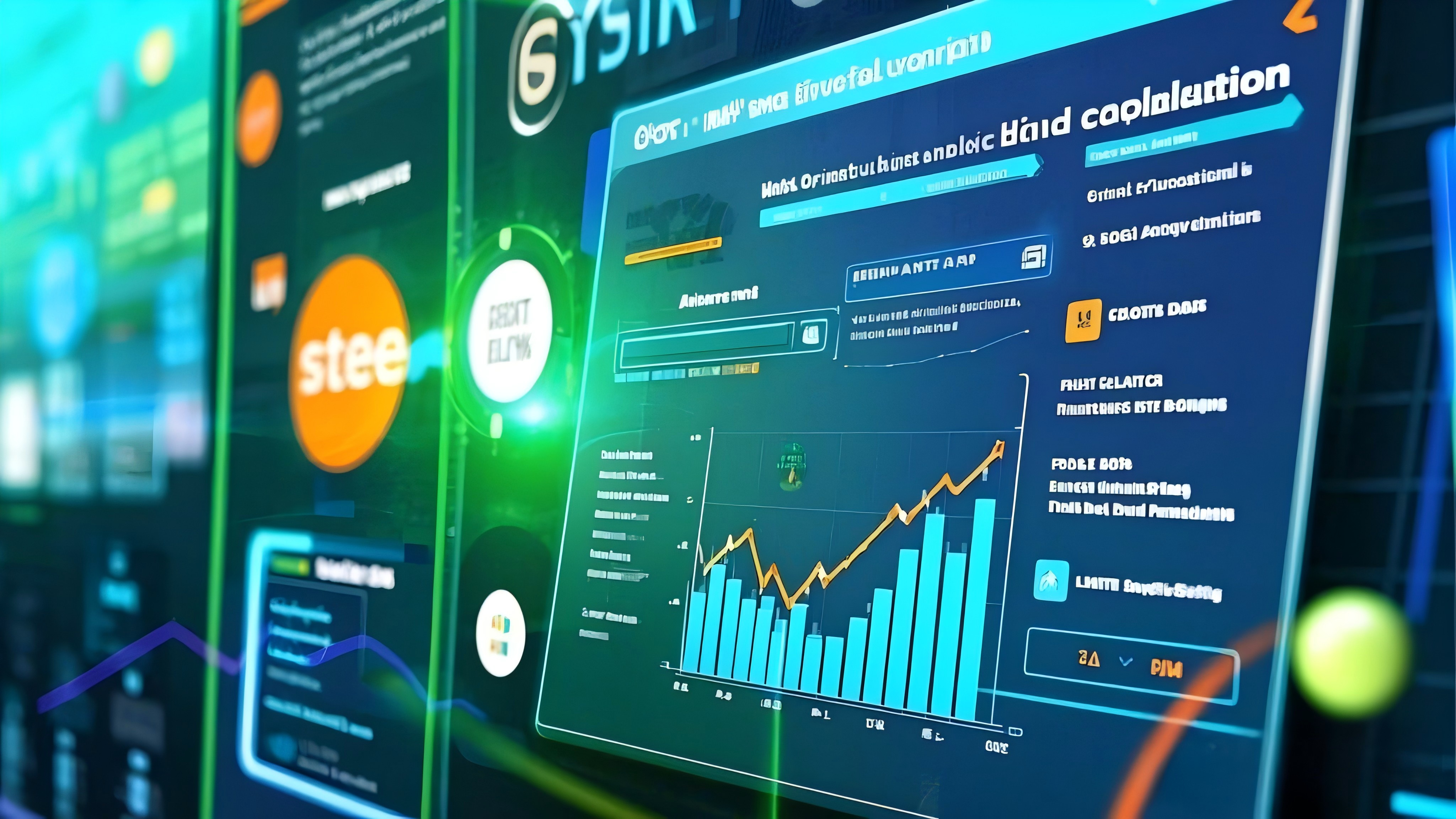
We hope this blog provides valuable insights into the mining supply chain and the critical role of ore blending.
If you have any questions or feedback, feel free to leave a comment!
By adopting MixOrePlan, the mining industry can achieve greater efficiency, cost savings, and sustainability.
Stay tuned for more updates and innovations from MixOrePlan!
Note: All images and data used in this article are for illustrative purposes only.